About Us
Textiles constitute an obvious choice as multifunctional platforms, since they are worn and used to cover and drape over many of the surfaces around us. Textiles serve as a natural interface between us and the environment in which we live. Textile products offer tremendous potential to functionalize and deploy sensors, actuators, and other devices at various hierarchical levels (from molecules to products) to engender intelligent attributes of self-monitoring, adaptation, responsiveness, and others.
The SmARTextiles Lab carries out research in various fields of textile engineering and technology, and fibers and polymer science, including:
- Fibrous actuators and sensors
- Mechanically gradient electroactive composites
- Mechanics of fibrous assemblies
- Electronic Textiles or E-textiles (Fiber/Textile based electrical devices)
- Electroactive polymers
- Design and analysis of technical textiles
- Dynamics of textile processes
- Technology of fabric formation, in particular, weaving technology
Testing Capabilities
SMARTextiles Laboratory, located in the College of Textiles Complex on NCSU’s Centennial campus, is the hub of smart/intelligent textile related research activity at NCSU. The Nanocomposite Fabrication Facility in the laboratory is equipped with a high shear planetary mixer/deaerator, spin coater, various sonicators, vacuum oven, and fume hood. The electro-mechanical characterization capabilities in the laboratory include a load frame (MTS 30G) with a range of load cells and grip types, optical non-contact type strain measurement equipment, a wide range of electrical test equipment including various electrometers, current-Voltage source/meters (Keithley 6221, 2182 A, 6517B, 8009, etc.), high voltage power supplies (Bertan High Voltage Power Supply Series 225, Series 220), and oscilloscopes.
Recently Completed and Current Research Projects
Dynamic Analysis of Ring Spinning and Over-end Unwinding Processes
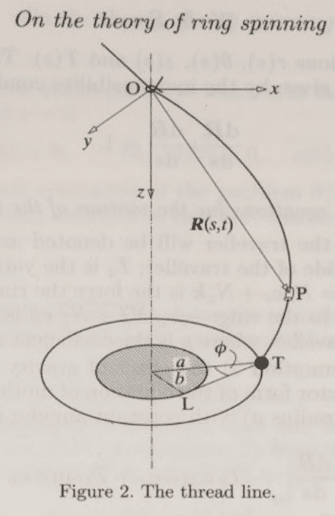
At the beginning of my tenure at NC State my research focus was mainly on process simulation as it relates to ring spinning and over-end unwinding. Initially, I worked with my colleague at the college, Profs. Subhash Batra and M. Zeidman. Later the team also included Prof. Barrie Fraser of the School of Mathematics and Statistics of the University of Sydney. In ring spinning, we developed analytical and subsequently computational models to explain the shape, tension distribution, and stability of the balloon as a function of the spinning geometry bobbin radius, balloon height, etc.), traveler mass, and speed with or without consideration of air-drag. The theory was finally modified to show the effects of the control ring. In unwinding, we provided a theoretical framework using a regular perturbation expansion to approximate the time dependence of the moving boundary condition (at the unwinding point). The method helped explain the relationship between yarn movements on and off the package during unwinding and thereby obtain the solution of the problem with appropriate continuity between solutions. The research results published in twelve papers are considered some of the most important in this area.
Electroactive Nanostructured Polymers as Tunable Actuators
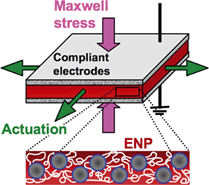
The first of my notable research collaborations is that with Prof. Richard Spontak, of the Chemical and Biomolecular Engineering Department of NC State. My interaction with Prof. Spontak began in mid-2005 after I returned from an SPIE conference on polymer actuators and invited Prof. Spontak to a casual lunch-time conversation on my interest in the evolving research area of dielectric electroactive polymers and textiles. The discussion soon produced two significant research grants (NSF and National Textile Center), and many years of intense and very productive collaborative work on exploring the electroactive behavior of nanostructued elastomer gels. It led to the development of a new class of electroactive dielectric elastomers, thermoplastic elastomer gels that are readily tunable to a wide spectrum of electromechanical properties. The materials we developed, exhibit high levels of actuation strain (up to ~300% area strain) under relatively low electric fields (as low as ~20 V/m) with negligible strain hysteresis and comparable energy density, efficiency, and damping as human muscles. We demonstrated the use of nanostructured polymers whose properties can be broadly tailored by varying copolymer characteristics or blend composition represents an innovative and tunable avenue to reduced-field actuation for advanced engineering, biomimetic, and biomedical applications. Along the way, the research produced four doctoral dissertations, and 12 peer-reviewed research papers in high impact journals.
Fiber-based Multimodal Sensors
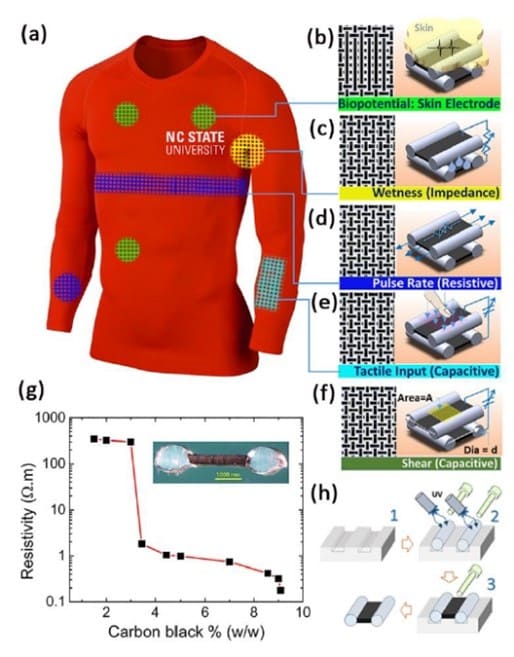
The second example comes from my research collaboration with Prof. Alper Bozkurt of the ECE department on the study of fiber-based electronics. Once again, I initiated the conversation with Prof. Bozkurt on some of my ideas in the emerging field of electronic textiles (e-textiles) back in 2011. Once the research ideas took shape and we began generating some data, we received funding from NC State’s Chancellor’s Innovation Fund and two back-to-back research grants from the NSF. The second NSF grant had two additional PIs, one from NC State and the other from UNC, Chapel Hill. In this ongoing research, we are developing a transformative technology through the design of a multimodal and multifunctional sensor array formed within a woven fabric structure using extrusion printed bicomponent fibers. Our fibers are able to measure tactile (compressive), tensile, shear deformations, as well as wetness of the fiber assembly through capacitive and/or resistive measurement. The exceptional strength of our approach is in its facile scalability and its potential to manufacture from a wide variety of materials using simple and time-tested industrial processes. Our sensory fibers can be manufactured using commercial bicomponent melt extrusion systems and can be easily assembled into sensor arrays using a commercial roll-to-roll weaving process, thus allowing a simple, cheap, yet robust sensing platform for high-performance, large-area e-textile sensors. We currently have five doctoral students working on the project, and we have already published eight peer-reviewed research papers.
Bioinspired Electrically Activated Soft Bistable Actuators
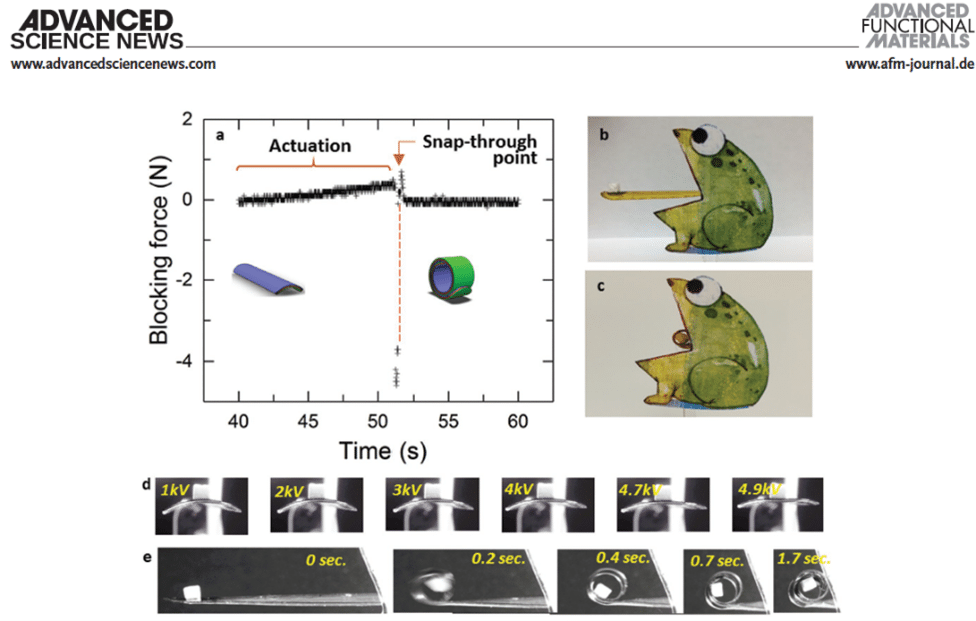
More recently, I have made the study of biomimetic actuation and control the central focus of my research. Movement and morphing in biological systems provide insights into the materials and mechanisms that may enable the development of advanced engineering structures. The nastic motion of plants in response to environmental stimuli, e.g., the rapid closure of the Venus flytrap’s leaves, utilizes snap-through instabilities originating from anisotropic deformation of plant tissues. In contrast, ballistic tongue projection of chameleon is attributed to direct mechanical energy transformation by stretching elastic tissues in advance of rapid projection to achieve higher speed and power output. In this instance, I began working with Prof. Douglas P. Holmes of the Department of Mechanical Engineering, Boston University at the beginning of 2016. Prof. Holmes is a well-known expert in the mechanics of slender and soft structures like rods, plates, and shells. Our primary objective in this research has been to utilize electrically active polymers for the controlled deformation and buckling of thin structures to control shape fluid flow. We believe a fundamental understanding of the bistability and control of these shapes will open up new opportunities in textile-based devices and systems for comfort and protection. In a recently published work, we demonstrated a bioinspired trilayered bistable all-polymer laminate containing dielectric elastomers (DEs) is reported, which double as both structural and active materials. It is demonstrated that the prestress and laminating strategy induces tunable bistability, while the electromechanical response of the DE-film enables reversible shape transition and morphing. Electrical actuation of bistable structures obviates the need for continuous application of electric field to sustain their transformed state. The experimental results are qualitatively consistent with our theoretical analyses of prestrain-dependent shape and bistability.
Functionally Tailored Textiles: 3-D Structures Through Melt Blown Technology
The research is aimed at developing appropriate technology necessary to produce three-dimensional molded garments to produce low-cost combat uniforms with effective barrier characteristics, using minimal joining. The system being developed is called Robotic Fiber Assembly and Control (RFAC) system. RFAC system will allow the incorporation of fibers, powders, or other appropriate additives into the garment systems. The additives may identify, measure, absorb, and/or deactivate chemical/biological agents. In the RFAC system deposition of melt-blown fibers on an appropriate mold is controlled by a six-axis industrial robot. The system allows precise control of fiber orientation distribution, fiber diameter distributions, and pore size distribution.
Development of Fiber Actuators
Fiber actuators are capable of dimensional change under the applied electrical field. Dielectric elastomer-based prototype fiber actuators have been developed using commercially available dielectric elastomer tubes and by applying appropriate compliant electrodes to the inner cavity and outer walls of these tubes. The force and displacement generated by such actuators have been studied under different isometric conditions and as a function of the applied electric field. The actuation characteristics such as axial strains, radial strains, and actuation blocking forces produced in the prototype upon actuation were studied. Actuation strain and blocking force are strongly influenced by the applied prestrain and have a parabolic relationship to the applied electric field. High actuation strains (>50%) are currently afforded by dielectric elastomers at relatively high electric fields (>50 V/µm). A new class of electroactive polymers, suitable for fiber formation, have been developed by incorporating low-volatility, aliphatic-rich solvent into a nanostructured triblock copolymer yielding physically crosslinked micellar networks that exhibit excellent displacement under an external electric field. Ultrahigh areal actuation strains (>200%) at significantly reduced electric fields (<40 V/µm) has been achieved.
Woven Fabric-based Electrical Circuits (Electro-textiles)
Fabric-based electrical circuits are fundamental to electronic textile products of the future. The objective of the current research is to develop fabric-based electrical circuits by interlacing conducting and non-conducting threads into woven textile structures for civilians as well as military applications. Wired interconnections between different devices attached to the conducting elements of these circuits are made by weaving conductive threads so that they follow desired electrical circuit designs. In a woven electrically conductive network, routing of electrical signals is achieved by the formation of effective electrical interconnects and disconnects. Resistance welding is identified as one of the most effective means of producing crossover point interconnects and disconnects. These circuits are evaluated for signal integrity issues (crosstalk, etc.). Two new thread structures – coaxial and twisted Pair copper threads to minimize cross talk have been developed and evaluated. Significant reductions in crosstalk were obtained with the coaxial and twisted pair thread structures when compared with bare copper thread or insulated conductive threads.
Carbon Nanofiber-Modified PVC as Fabric Sensor Composites for E-Textiles
The research aims to use screen-printing to fabricate an elastic and conductive nanocomposite layer of Plastisol, plasticized poly(vinyl chloride) (PVC), and carbon nanofiber (CNF) on textile fabrics to produce a piezoresistive strain-sensing substrate. The fabric sensor composite (FSC) being developed is based on the hypothesis that an elastomeric layer containing conducting nanoparticles printed on fabric substrates can yield a flexible, piezoresistive coating that can be tailored for specific applications. The research marries the demonstrated utility of plastisol as a print medium with the novelty of CNF-based polymer nanocomposites as applied to FSCs designed for use in electronic textiles. Previous studies have repeatedly identified benefits of CNFs relative to their CNT analogs, but relatively few studies have focused on conformable nanocomposites containing CNFs. The work seeks to establish a fundamental understanding of the physical factors governing CNF dispersion, percolation and subsequent mobility (upon drying) in a solvated polymer system (plastisol print medium) as a necessary prerequisite to the rational development of the target FSC. Insight into the percolation behavior of CNFs embedded in plastisol and subsequent property evolution will help to elucidate and further optimize the piezoresistive behavior of the FSC. Thus far, the percolation threshold of the plastisol-CNF was observed to be at ~2wt% and that the concentration of CNF where the resistivity starts to saturate is observed to be at 5wt%. Another significant observation is the increase of about 8 orders of magnitude in the conductivity of the composite when the concentration of the CNF was increased from 2wt % to 5wt %.